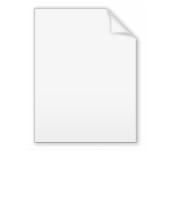
Cellulose insulation
Encyclopedia
The word cellulose
comes from the French word for a living cellule and glucose
, which is sugar. Building insulation
is low-thermal-conductivity
material used to separate the internal climate and sounds of a building from external climate and sounds. Cellulose insulation is plant fiber used in wall and roof cavities to separate the inside and outside of the building thermally and acoustically.
. Many types of cellulosic materials have been used, including newspaper, cardboard, cotton, straw, sawdust, hemp and corncob. Monticello
was insulated with a form of cellulose. Modern cellulose insulation, made with recycled newspaper using grinding and dust removing machines and adding a fire retardant, began in the 1950s and came into general use in the US during the 1970s.
The market for insulation increased following the oil embargo of 1973-74. The embargo caused energy costs for heating to skyrocket across the nation, which led to increased interest in energy conservation measures. Insulation gained significant national attention as a cheap and available technology to increase the energy efficiency of homes. In 1977, following a particularly severe winter, a tax credit was given for homeowners who installed insulation.
While in 1976 there were roughly 100 cellulose insulation firms with 125 plants, by 1978 there were more than 350 firms with more than 500 plants1. Cellulose insulation was produced locally by small manufacturers who purchased ready-to-operate machines and offered a cheap and easy low-tech production process. Other than some constraints created by a shortage of boric acid for use as fire retardant, cellulose captured an increased share of the market due to lower costs and its suitability for retrofits. Meanwhile fiberglass and rockwool producers found it difficult to keep up with the demand for insulation from their customers.
Due to complaints by retailers, contractors and consumers about price, safety and quality control problems, the federal government began enacting insulation standards beginning in 1978. There was a great concern that the growth in cellulose manufactures was leading to improperly or insufficiently treating insulation against the threat of fire even though reliable statistics on a national basis did not exist. This led to the Federal Consumer Products Safety Commission passing 16 CFR Part 1209, which sets safety standards covering four product attributes for cellulose insulation only: settled density, corrosiveness, critical radiant flux and smoldering combustion. Another regulation passed was the “R-value
Rule,” placing clear limitations on the claims that manufacturing and marketing firms can make about their product.
The effect of regulations by the CPSC put most of the small producers of cellulose insulation out of business. The costs incurred by increasing fire testing made cellulose more expensive and the bad publicity helped decrease demand. They were either unable to meet the testing requirements or they merged with other small manufacturers. In 1985 the CPSC asked Congress to repeal the flammability standard after further studies. By 1991 only 61 cellulose producers still remained in the US.
The fiberglass industry meanwhile benefited from most of the regulations passed by the federal government. The heavy lobbying by the more centralized fiberglass
and mineral insulation manufacturers helped pass the tough fire standards for cellulose insulation. These standards were reinforced by technical bulletins published by the Mineral Insulation Manufacturers Association (currently known as the North American Insulation Manufacturers Association) that promoted fire hazard claims against cellulose insulation. These claims were not independently verified, faced little scientific review, and were misleading and untrue.
Currently cellulose insulation has increased again in use in the United States. Part of the reason for this growth are studies that have shown results that suggest that cellulose may actually protect a building from damage in a fire better than fiberglass because cellulose is denser than fiberglass and doesn't allow the oxygen necessary to burn structural members. Several National Research Council Canada studies
http://irc.nrc-cnrc.gc.ca/pubs/fulltext/ir806/ have backed these claims. Another major reason for the comeback of cellulose might be because of the increased interest in green building
. Cellulose has the highest recycled content of any insulation material and also has less embodied energy
than fiberglass and other furnace produced mineral insulations.
Loose fill in walls is an antiquated technique of using cellulose in wall cavities. The home performance industry and its accrediting bodies support the dense-pack standard of insulating wall cavities, which does not settle. This method stops the stack effect and convective loops in wall cavities.
of 3.8 per inch) which is about the same as or slightly better than glass wool or rock wool. This doesn’t represent the whole picture of thermal performance. Other important aspects are how well the building envelope is sealed from air infiltration, convective airflows, and thermal bridging.
Cellulose is very good at fitting around items in walls like pipes and wiring, leaving few air pockets that can reduce the overall efficiency of the wall. Dense pack cellulose can seal walls from air infiltration while providing the density to limit convection, when installed properly. The University of Colorado School of Architecture and Planning did a study that compared two seemingly identical test structures, one with cellulose and the other with fiberglass. The cellulose structure had used 26.4% less energy to heat. It also was shown to tighten the structure more than 30%. Subsequent real world surveys have cellulose performing 20-30% better at reducing energy used for heating than fiberglass.
Compared to foam insulation, cellulose has a lower R-value per inch, but is much less expensive; foam has a higher cost per equivalent R-value. (needs citation)
Several installation options allow walls to have a Sound Transmission Class
(STC) of 50 or greater. As a comparison, walls with fiberglass batts have an STC of 36-39, depending on stud and screw spacing.
It is a common misconception that the mere presence of crude borates in cellulose insulation provides pest control properties to the product. While boric acid itself does kill self-grooming insects if ingested, it must be presented to an insect in both sufficient concentration and in an ingestible form in order to achieve insect fatality. Proper testing of products containing borates must be performed in order to determine whether dosage and presentation are sufficient to kill insects. Once tested, registration with the EPA as a pesticide is required before a product may be touted as having pesticidal capabilities.
and borate. Although ammonium sulfate is normally odorless, unexplained emission of ammonia and a resulting ammonia smell has been found in some cases.
In addition, cellulose acts to distribute moisture throughout the cavity, preventing the buildup of moisture in one area and helping to dry the moisture more quickly. Cellulose manufacturers do not recommend the installation of a vapor barrier with cellulose.
Most city codes will require a vapor barrier for any external wall. Most US cities will consider an appeal of the requirement if proper reasoning is provided. In March 2008 The US city of Portland, Oregon, approved an appeal to waive the requirement for a vapor barrier/retarder when using cellulose insulation. The appeal can be viewed in the Portland Bureau of Development Services search form by searching for appeal ID 4996. Fundamental to any appeal is mentioning that recent studies show air movement is the primary problem for vapor, that cellulose is an effective barrier to air movement, and that cellulose acts to diffuse vapor.
HFC.
As with other non-batt insulation, city and regional/state building codes may not be updated for cellulose insulation. Homeowners should call the city to verify that the insulation will be approved, and it may be necessary to provide product specifications to the city. This is not difficult, and the installer and the manufacturer should both be willing to handle this process, saving the homeowner any true effort.
Most building codes require a vapor barrier, and it can be hard to convince some cities that one is not required for cellulose. In this case, an appeal (usually a quick process) may be necessary. Otherwise, vapor barriers can be installed. Options for a vapor barrier include plastic sheeting (fairly low environmental footprint due to the thin layer needed) or PVA paint (contains toxins and other qualities undesirable from an environmental standpoint).
or ammonium sulphate. Cellulose has the highest recycled content of any insulation available. For example, fiberglass has a maximum amount of 30% recycled content.
hundred or thousands of times higher than that of carbon dioxide, cellulose does not produce significant gaseous emissions. Unlike fiberglass, cellulose does not use formaldehyde
-based glues, which present a continuing hazard after installation due to off-gassing of formaldehyde.
Cellulose has great advantages for industrial health and worker safety. Toxicity of the raw materials of most insulation types is typically highest during manufacture or installation. Neither is an issue with cellulose.
The sole hazard of cellulose according to the categorization by the OSHA
is that it is a dust nuisance, requiring a simple dust mask during installation. This compares very favorably to the potential NIOSH cancer risk of fiberglass
of cellulose compared to all other insulation is by far the lowest. It requires 20 to 40 times as much energy to produce furnace-made insulation materials compared to cellulose. Cellulose is made by electrically powered machines while mineral insulation is made in furnaces. Cellulose is also made with locally available materials other than the fire retardant, while mineral insulation factories have to ship materials and products over greater distances.
Cellulose insulation uses borates for fire retardation. Borates are a non-renewable mined product.
is about as dangerous as table salt . There is slight concern over the off gassing of ink from the newspapers but the material is sealed behind walls, and no studies have shown this as an issue.
Cellulose
Cellulose is an organic compound with the formula , a polysaccharide consisting of a linear chain of several hundred to over ten thousand β linked D-glucose units....
comes from the French word for a living cellule and glucose
Glucose
Glucose is a simple sugar and an important carbohydrate in biology. Cells use it as the primary source of energy and a metabolic intermediate...
, which is sugar. Building insulation
Building insulation
building insulation refers broadly to any object in a building used as insulation for any purpose. While the majority of insulation in buildings is for thermal purposes, the term also applies to acoustic insulation, fire insulation, and impact insulation...
is low-thermal-conductivity
Thermal conductivity
In physics, thermal conductivity, k, is the property of a material's ability to conduct heat. It appears primarily in Fourier's Law for heat conduction....
material used to separate the internal climate and sounds of a building from external climate and sounds. Cellulose insulation is plant fiber used in wall and roof cavities to separate the inside and outside of the building thermally and acoustically.
History of cellulose insulation
Cellulose is the oldest building insulation materialBuilding insulation materials
Building insulation materials are thermal insulation used in the construction or retrofit of buildings.The materials are used to reduce heat transfer by conduction, radiation or convection and are employed in varying combinations to achieve the desired outcome .-Categories:Insulation may be...
. Many types of cellulosic materials have been used, including newspaper, cardboard, cotton, straw, sawdust, hemp and corncob. Monticello
Monticello
Monticello is a National Historic Landmark just outside Charlottesville, Virginia, United States. It was the estate of Thomas Jefferson, the principal author of the United States Declaration of Independence, third President of the United States, and founder of the University of Virginia; it is...
was insulated with a form of cellulose. Modern cellulose insulation, made with recycled newspaper using grinding and dust removing machines and adding a fire retardant, began in the 1950s and came into general use in the US during the 1970s.
The market for insulation increased following the oil embargo of 1973-74. The embargo caused energy costs for heating to skyrocket across the nation, which led to increased interest in energy conservation measures. Insulation gained significant national attention as a cheap and available technology to increase the energy efficiency of homes. In 1977, following a particularly severe winter, a tax credit was given for homeowners who installed insulation.
While in 1976 there were roughly 100 cellulose insulation firms with 125 plants, by 1978 there were more than 350 firms with more than 500 plants1. Cellulose insulation was produced locally by small manufacturers who purchased ready-to-operate machines and offered a cheap and easy low-tech production process. Other than some constraints created by a shortage of boric acid for use as fire retardant, cellulose captured an increased share of the market due to lower costs and its suitability for retrofits. Meanwhile fiberglass and rockwool producers found it difficult to keep up with the demand for insulation from their customers.
Due to complaints by retailers, contractors and consumers about price, safety and quality control problems, the federal government began enacting insulation standards beginning in 1978. There was a great concern that the growth in cellulose manufactures was leading to improperly or insufficiently treating insulation against the threat of fire even though reliable statistics on a national basis did not exist. This led to the Federal Consumer Products Safety Commission passing 16 CFR Part 1209, which sets safety standards covering four product attributes for cellulose insulation only: settled density, corrosiveness, critical radiant flux and smoldering combustion. Another regulation passed was the “R-value
R-value (insulation)
The R-value is a measure of thermal resistance used in the building and construction industry. Under uniform conditions it is the ratio of the temperature difference across an insulator and the heat flux through it or R = \Delta T/\dot Q_A.The R-value being discussed is the unit thermal resistance...
Rule,” placing clear limitations on the claims that manufacturing and marketing firms can make about their product.
The effect of regulations by the CPSC put most of the small producers of cellulose insulation out of business. The costs incurred by increasing fire testing made cellulose more expensive and the bad publicity helped decrease demand. They were either unable to meet the testing requirements or they merged with other small manufacturers. In 1985 the CPSC asked Congress to repeal the flammability standard after further studies. By 1991 only 61 cellulose producers still remained in the US.
The fiberglass industry meanwhile benefited from most of the regulations passed by the federal government. The heavy lobbying by the more centralized fiberglass
Fiberglass
Glass fiber is a material consisting of numerous extremely fine fibers of glass.Glassmakers throughout history have experimented with glass fibers, but mass manufacture of glass fiber was only made possible with the invention of finer machine tooling...
and mineral insulation manufacturers helped pass the tough fire standards for cellulose insulation. These standards were reinforced by technical bulletins published by the Mineral Insulation Manufacturers Association (currently known as the North American Insulation Manufacturers Association) that promoted fire hazard claims against cellulose insulation. These claims were not independently verified, faced little scientific review, and were misleading and untrue.
Currently cellulose insulation has increased again in use in the United States. Part of the reason for this growth are studies that have shown results that suggest that cellulose may actually protect a building from damage in a fire better than fiberglass because cellulose is denser than fiberglass and doesn't allow the oxygen necessary to burn structural members. Several National Research Council Canada studies
http://irc.nrc-cnrc.gc.ca/pubs/fulltext/ir806/ have backed these claims. Another major reason for the comeback of cellulose might be because of the increased interest in green building
Green building
Green building refers to a structure and using process that is environmentally responsible and resource-efficient throughout a building's life-cycle: from siting to design, construction, operation, maintenance, renovation, and demolition...
. Cellulose has the highest recycled content of any insulation material and also has less embodied energy
Embodied energy
Embodied energy is defined as the sum of energy inputs that was used in the work to make any product, from the point of extraction and refining materials, bringing it to market, and disposal / re-purposing of it...
than fiberglass and other furnace produced mineral insulations.
Products
Four major types of loose-fill cellulose products have been developed under a variety of brand names. These are generally characterized as dry cellulose, spray applied cellulose, stabilized cellulose, and low dust cellulose. These types are used in different parts of a building and for different reasons.Dry cellulose (loose fill)
Dry cellulose is used in retrofitting old homes by blowing the cellulose into holes drilled into the tops of the walls. It can also be blown into a new wall construction by using temporary retainers or netting that is clamped in place then removed once the cellulose has reached the appropriate density. This form of application does settle as much as 20% but the stated R-value of the cellulose is accurate after settling occurs. In addition, a dense-pack option can be used to reduce settling and further minimize air gaps. Dense-pack places pressure on the cavity, and should be done by an experienced installer.Loose fill in walls is an antiquated technique of using cellulose in wall cavities. The home performance industry and its accrediting bodies support the dense-pack standard of insulating wall cavities, which does not settle. This method stops the stack effect and convective loops in wall cavities.
Spray-applied cellulose (wet-spray cellulose)
Spray-applied cellulose is used for applying cellulose to new wall construction. The differences are the addition of water to the cellulose while spraying as well as adding some kind of moisture retardant such as chlorine to prevent mold cultures. In some cases the insulation might also mix in a very small percentage of adhesive or activate a dry adhesive present in the cellulose. Wet-spray allows application without the need for a temporary retainer. In addition, wet-spray allows for an even better seal of the insulated cavity against air infiltration and eliminates settling problems. Wet-spray installation requires that the wall be allowed to dry for a minimum of 24 hours (or until maximum of 25% moisture is reached) before being covered.Stabilized cellulose
Stabilized cellulose is used most often in attic/roof insulation. It is applied with a very small amount of water to activate an adhesive of some kind. This reduces settling and decreases the amount of cellulose needed. This can prove advantageous at reducing the overall weight of the product on the ceiling drywall helping prevent possible sag. This application is ideal for sloped roofs and has been approved for 5:12 (41.66%) slopes.Low-dust cellulose
The last major type of cellulose insulation on the market is low-dust variety. Nuisance levels of dust are created during application of most types of dry insulation causing the need for simple dust masks to be worn during installation. This kind of cellulose has a small percentage of oil or similar dust dampener added. This may also be appropriate to homes where people are sensitive to newsprint or paper dust (though new dust will not be created after installation).Thermal performance
The thermal performance of loose filled cellulose compares favorably to other types of insulation. The thermal conductivity of loose-fill cellulose is approximately 40 mW/m·K (an R-valueR-value (insulation)
The R-value is a measure of thermal resistance used in the building and construction industry. Under uniform conditions it is the ratio of the temperature difference across an insulator and the heat flux through it or R = \Delta T/\dot Q_A.The R-value being discussed is the unit thermal resistance...
of 3.8 per inch) which is about the same as or slightly better than glass wool or rock wool. This doesn’t represent the whole picture of thermal performance. Other important aspects are how well the building envelope is sealed from air infiltration, convective airflows, and thermal bridging.
Cellulose is very good at fitting around items in walls like pipes and wiring, leaving few air pockets that can reduce the overall efficiency of the wall. Dense pack cellulose can seal walls from air infiltration while providing the density to limit convection, when installed properly. The University of Colorado School of Architecture and Planning did a study that compared two seemingly identical test structures, one with cellulose and the other with fiberglass. The cellulose structure had used 26.4% less energy to heat. It also was shown to tighten the structure more than 30%. Subsequent real world surveys have cellulose performing 20-30% better at reducing energy used for heating than fiberglass.
Compared to foam insulation, cellulose has a lower R-value per inch, but is much less expensive; foam has a higher cost per equivalent R-value. (needs citation)
Long-term cost savings
Cellulose's insulation qualities "can save homeowners 20 to 50 percent on their utility bills".Sound insulation
Noise reduction is achieved in three ways with cellulose. The first is that cellulose completely fills cavities leaving few air pockets for sound to travel in. The second is the cellulose material's ability to trap air. The significant difference between noise reduction with cellulose and fiberglass is its density. Cellulose is approximately three times denser then fiberglass. This helps deaden the sound through walls and between floor levels.Several installation options allow walls to have a Sound Transmission Class
Sound transmission class
Sound Transmission Class is an integer rating of how well a building partition attenuates airborne sound. In the USA, it is widely used to rate interior partitions, ceilings/floors, doors, windows and exterior wall configurations . Outside the USA, the Sound Reduction Index ISO standard is used...
(STC) of 50 or greater. As a comparison, walls with fiberglass batts have an STC of 36-39, depending on stud and screw spacing.
Mold and pest control
The borates in cellulose insulation provide superior control against mold. Installations have shown that even several months of water-saturation and improper installation did not result in mold.It is a common misconception that the mere presence of crude borates in cellulose insulation provides pest control properties to the product. While boric acid itself does kill self-grooming insects if ingested, it must be presented to an insect in both sufficient concentration and in an ingestible form in order to achieve insect fatality. Proper testing of products containing borates must be performed in order to determine whether dosage and presentation are sufficient to kill insects. Once tested, registration with the EPA as a pesticide is required before a product may be touted as having pesticidal capabilities.
Fire retardation
The borate treatment also gives cellulose the highest (Class I) fire safety rating. Many cellulose companies use a blend of ammonium sulfateAmmonium sulfate
Ammonium sulfate , 2SO4, is an inorganic salt with a number of commercial uses. The most common use is as a soil fertilizer. It contains 21% nitrogen as ammonium cations, and 24% sulfur as sulfate anions...
and borate. Although ammonium sulfate is normally odorless, unexplained emission of ammonia and a resulting ammonia smell has been found in some cases.
Vapor barrier
A vapor barrier may not be needed with cellulose insulation. For example, recent studies have shown that air movement is the primary method by which excessive moisture can accumulate in mild marine climate such as Portland, OR, USA. An insulation that fills the wall cavity completely (such as cellulose or foam) can help prevent moisture problems. Recommendations against using vapor barriers with cellulose insulation are supported by studies, even though they classify cellulose as vapor permeable.In addition, cellulose acts to distribute moisture throughout the cavity, preventing the buildup of moisture in one area and helping to dry the moisture more quickly. Cellulose manufacturers do not recommend the installation of a vapor barrier with cellulose.
Most city codes will require a vapor barrier for any external wall. Most US cities will consider an appeal of the requirement if proper reasoning is provided. In March 2008 The US city of Portland, Oregon, approved an appeal to waive the requirement for a vapor barrier/retarder when using cellulose insulation. The appeal can be viewed in the Portland Bureau of Development Services search form by searching for appeal ID 4996. Fundamental to any appeal is mentioning that recent studies show air movement is the primary problem for vapor, that cellulose is an effective barrier to air movement, and that cellulose acts to diffuse vapor.
Disadvantages
Cellulose has few disadvantages. As compared to other insulation options, the R-value of 3.6 to 3.8 per inch is very good but not the best (though it competes well in cost per R-value). Spray foam has many of the same benefits as wet-spray cellulose (such as sealing the cavity), while having advantages in R-value and rigidity and air sealing. However, many spray foams utilize an environmentally harmful blowing agent, such as EnovateEnovate
A proprietary foam insulation blowing agent produced by Honeywell used in closed-cell spray foam insulation. Enovate is also known as HFC-245fa, or 1,1,1,3,3,-pentafluoropropane. Unlike CFC and HCFC blowing agents formerly used for this purpose, it has zero ozone depletion potential. However, it...
HFC.
Dust
Cellulose is prone to create too much dust that is blown into the house through inadequate seals around fixtures or minute holes. This is mostly found in rooms that are used frequently and can be a real health problem, especially if you live in a carpet-less home where dust stays airborne longer. Even those old constructions with tiny holes in the wall, may cause the cellulose dust to be blown into the rooms. This is one of the major blown cellulose insulation problems. Also, removal can be very costly depending on square footage.Installation expertise and building codes
In some areas it can be difficult to locate installers that are experienced with cellulose. An experienced installer understands how to correctly dense-pack loose fill dry cellulose, how to best apply stabilized (partly wet) cellulose on sloped surfaces, and the proper time required for wet-spray cellulose to dry.As with other non-batt insulation, city and regional/state building codes may not be updated for cellulose insulation. Homeowners should call the city to verify that the insulation will be approved, and it may be necessary to provide product specifications to the city. This is not difficult, and the installer and the manufacturer should both be willing to handle this process, saving the homeowner any true effort.
Most building codes require a vapor barrier, and it can be hard to convince some cities that one is not required for cellulose. In this case, an appeal (usually a quick process) may be necessary. Otherwise, vapor barriers can be installed. Options for a vapor barrier include plastic sheeting (fairly low environmental footprint due to the thin layer needed) or PVA paint (contains toxins and other qualities undesirable from an environmental standpoint).
Wet-spray drying time
Wet-spray provides the advantage of a better sealing of the insulated cavity and superior rigidity. However, the moisture from a wet-spray insulation requires a longer drying time before the drywall/sheet-rock is applied to a newly insulated wall. This drying time is usually reduced by the use of large space heaters that are run for a few days to weeks, depending on ambient humidity. The installer should use a moisture meter to verify acceptable in-wall moisture levels before any drywall is applied. From an environmental and energy efficiency perspective, wet-spray is well worth the extra heating and time. This extra timing needs to be considered as part of the building schedule for new or remodel projects.Weight
For a given R-value, loose cellulose weighs roughly three times as much per square foot as loose fiberglass. Ceiling structures should be inspected for signs of weakness before choosing a material for insulating the ceilings of existing structures.Sustainable and environmentally preferable properties
Cellulose insulation is growing in popularity, in part due to being one of the most environmentally preferable insulation types available.Recycled content
Cellulose is composed of 75-85% recycled paper fiber, usually post-consumer waste newsprint. The other 15% is a fire retardant such as boric acidBoric acid
Boric acid, also called hydrogen borate or boracic acid or orthoboric acid or acidum boricum, is a weak acid of boron often used as an antiseptic, insecticide, flame retardant, as a neutron absorber, and as a precursor of other chemical compounds. It exists in the form of colorless crystals or a...
or ammonium sulphate. Cellulose has the highest recycled content of any insulation available. For example, fiberglass has a maximum amount of 30% recycled content.
Low toxicity and environmental impact of raw materials
The non-recycled components of cellulose insulation are still environmentally preferable to the raw materials of most other insulation types, which are often petrochemical-based (this includes foam and fiberglass). Unlike foam insulations, many of which use HFC or HCFC blowing agents which have global warming potentialGlobal warming potential
Global-warming potential is a relative measure of how much heat a greenhouse gas traps in the atmosphere. It compares the amount of heat trapped by a certain mass of the gas in question to the amount of heat trapped by a similar mass of carbon dioxide. A GWP is calculated over a specific time...
hundred or thousands of times higher than that of carbon dioxide, cellulose does not produce significant gaseous emissions. Unlike fiberglass, cellulose does not use formaldehyde
Formaldehyde
Formaldehyde is an organic compound with the formula CH2O. It is the simplest aldehyde, hence its systematic name methanal.Formaldehyde is a colorless gas with a characteristic pungent odor. It is an important precursor to many other chemical compounds, especially for polymers...
-based glues, which present a continuing hazard after installation due to off-gassing of formaldehyde.
Cellulose has great advantages for industrial health and worker safety. Toxicity of the raw materials of most insulation types is typically highest during manufacture or installation. Neither is an issue with cellulose.
The sole hazard of cellulose according to the categorization by the OSHA
Occupational Safety and Health Administration
The United States Occupational Safety and Health Administration is an agency of the United States Department of Labor. It was created by Congress of the United States under the Occupational Safety and Health Act, signed by President Richard M. Nixon, on December 29, 1970...
is that it is a dust nuisance, requiring a simple dust mask during installation. This compares very favorably to the potential NIOSH cancer risk of fiberglass
Embodied energy
The embodied energyEmbodied energy
Embodied energy is defined as the sum of energy inputs that was used in the work to make any product, from the point of extraction and refining materials, bringing it to market, and disposal / re-purposing of it...
of cellulose compared to all other insulation is by far the lowest. It requires 20 to 40 times as much energy to produce furnace-made insulation materials compared to cellulose. Cellulose is made by electrically powered machines while mineral insulation is made in furnaces. Cellulose is also made with locally available materials other than the fire retardant, while mineral insulation factories have to ship materials and products over greater distances.
Cellulose insulation uses borates for fire retardation. Borates are a non-renewable mined product.
Insulation is green
All insulation helps make buildings more energy efficient. Using cellulose insulation can contribute to obtaining LEED credits in the US Green Building Council certification program. It can earn credit in two categories: the energy and atmosphere energy performance category and the materials and resources recycled content category.Product safety
Cellulose insulation can be very dusty during insulation and it is recommended that a standard dust mask be worn while working. The fire retardant boric acidBoric acid
Boric acid, also called hydrogen borate or boracic acid or orthoboric acid or acidum boricum, is a weak acid of boron often used as an antiseptic, insecticide, flame retardant, as a neutron absorber, and as a precursor of other chemical compounds. It exists in the form of colorless crystals or a...
is about as dangerous as table salt . There is slight concern over the off gassing of ink from the newspapers but the material is sealed behind walls, and no studies have shown this as an issue.
External links
- The Cellulose Insulation Manufacturers' Association
- The Australian Cellulose Insulation Manufacturers' Association
- Bob Vila - Beach House Cellulose Installation Video
- This Old House - Retrofitting Cellulose Insulation video
- Is a Vapor Barrier Needed for a Cellulose Insulated Home?
- CIMA Technical Bulletin #2: Standard practice for installing cellulose building insulation