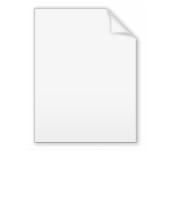
Cellular manufacturing
Encyclopedia
Cellular Manufacturing is a model for workplace design
, and has become an integral part of lean manufacturing
systems. Cellular Manufacturing is based upon the principals of Group Technology, which seeks to take full advantage of the similarity between parts, through standardisation and common processing. In Functional Manufacturing similar machines are placed close together (e.g. lathes, millers, drills etc.). Functional layouts are more robust to machine breakdowns, have common jigs and fixtures in the same area and supports high levels of demarcation. In Cellular Manufacturing systems machines are grouped together according to the families of parts produced. The major advantage is that material flow is significantly improved, which reduces the distance travelled by materials, inventory and cumulative lead times. Cellular Manufacturing employs setup reduction and gives the workers the tools to be multiprocess, operating multiple processes, and multifunctional, owning quality improvements, waste reduction, and simple machine maintenance. This allows workers to easily self-balance within the cell while reducing lead times, resulting in the ability for companies to manufacture high quality products at a low cost, on time, and in a flexible way.
The goal of lean manufacturing is the aggressive minimisation of waste, called muda, to achieve maximum efficiency of resources. Cellular manufacturing, sometimes called cellular or cell production, arranges factory floor labor into semi-autonomous and multi-skilled teams, or work cells, who manufacture complete products or complex components. Properly trained and implemented cells are more flexible and responsive than the traditional mass-production
line, and can manage processes, defects, scheduling, equipment maintenance, and other manufacturing issues more efficiently.
offers what by definition constitutes an early example of cellular manufacturing. By 1808, using machinery designed by Marc Isambard Brunel
and constructed by Henry Maudslay
, the Block Mills were producing 130,000 blocks (pulleys) for the Royal Navy
per year in single unit lots, with 10 men operating 42 machines arranged in three production flow lines. This installation apparently reduced manpower requirements by 90% (from 110 to 10), reduced cost substantially and greatly improved block consistency and quality. Group Technology
is a management strategy with long term goals of staying in business, growing, and making profits. Companies are under relentless pressure to reduce costs while meeting the high quality expectations of the customer to maintain a competitive advantage. Successfully implementing Cellular manufacturing allows companies to achieve cost savings and quality improvements, especially when combined with the other aspects of lean manufacturing. Cell manufacturing systems are currently used to manufacture anything from hydraulic and engine pumps used in aircraft to plastic packaging components made using injection molding.
While the machinery may be functionally dissimilar, the family of parts produced contains similar processing requirements or has geometric similarities. Thus, all parts basically follow the same routing with some minor variations (e.g., skipping an operation). The cells may have no conveyorized movement of parts between machines, or they may have a flow line connected by a conveyor that can provide automatic transfer.
In combination, each modular part is designed for a particular work cell, or dedicated clusters of machines or manufacturing processes. Cells are usually bigger than typical conventional workstations, but smaller than a complete conventional department. After conversion, a cellular manufacturing layout usually requires less floor space as a result of the optimized production processes. Each cell is responsible for its own internal control of quality, scheduling, ordering, and record keeping. The idea is to place the responsibility of these tasks on those who are most familiar with the situation and most able to quickly fix any problems. The middle management no longer has to monitor the outputs and interrelationships of every single worker, and instead only has to monitor a smaller number of work cells and the flow of materials between them, often achieved using a system of kanban
s.
The hard issues are a matter of design and investment. The entire factory floor is rearranged, and equipment is modified or replaced to enable cell manufacturing. The costs of work stoppages during implementation can be considerable, and lean manufacturing literature recommend that implementation should be phased to minimize the impacts of such disruptions as much as possible. The rearrangement of equipment (which is sometimes bolted to the floor or built into the factory building) or the replacement of equipment that is not flexible or reliable enough for cell manufacturing also pose considerable costs, although it may be justified as the upgrading obsolete equipment. In both cases, the costs have to be justified by the cost savings that can be realistically expected from the more flexible cell manufacturing system being introduced, and miscalculations can be disastrous. A common oversight is the need for multiple jigs, fixtures and or tooling for each cell. Properly designed, these requirements can be accommodated in specific-task cells serving other cells; such as a common punch press or test station. Too often, however, the issue is discovered late and each cell is found to require its own set of tooling.
The soft issues are more difficult to calculate and control. The implementation of cell manufacturing often involves employee training and the redefinition and reassignment of jobs. Each of the workers in each cell should ideally be able to complete the entire range of tasks required from that cell, and often this means being more multi-skilled than they were previously. For this reason, transition from a progressive assembly line type of manufacturing to cellular is often best managed in stages with both types co-existing for a period of time. In addition, cells are expected to be self-managing (to some extent), and therefore workers will have to learn the tools and strategies for effective teamwork and management, tasks that workers in conventional factory environments are entirely unused to. At the other end of the spectrum, the management will also find their jobs redefined, as they must take a more "hands-off" approach to allow work cells to effectively self-manage. Instead, they must learn to perform a more oversight and support role, maintaining a system where work cells self-optimize through supplier-input-process-output-customer (SIPOC) relationships. These soft issues, while difficult to pin down, pose a considerable challenge for cell manufacturing implementation; a factory with a cell manufacturing layout but without cell manufacturing workers and managers is unlikely to achieve the cell manufacturing benefits.
Product start-ups can be more difficult to manage if assembly training was traditionally accomplished station-by-station on a fixed assembly line. As each operator in a cell is responsible for a larger number of assembled parts and operations, the time needed to master the sequence and techniques is considerably longer. If multiple parallel cells are used, each cell must be launched separately (meaning slower production ramp) or with equal training resources (meaning more in total). The consideration of the cell's internal group dynamics, personalities and other traits is often more of a concern in cellular manufacturing due to the closer proximity and co-dependency of the team members; however properly implemented this is a major benefit of cellular manufacturing.
Part movement, set-up time, and wait time between operations are reduced, resulting in a reduction of work in progress inventory freeing idle capital that can be better utilized elsewhere. Cellular manufacturing, in combination with the other lean manufacturing and just-in-time processes, also helps eliminate overproduction by only producing items when they are needed. The results are cost savings and the better control of operations.
There are some costs of implementing cellular manufacturing, however, in addition to the set-up costs of equipment and stoppages noted above. Sometimes different work cells can require the same machines and tools, possibly resulting in duplication causing a higher investment of equipment and lowered machine utilization
. However, this is a matter of optimization and can be addressed through process design.
Design
Design as a noun informally refers to a plan or convention for the construction of an object or a system while “to design” refers to making this plan...
, and has become an integral part of lean manufacturing
Lean manufacturing
Lean manufacturing, lean enterprise, or lean production, often simply, "Lean," is a production practice that considers the expenditure of resources for any goal other than the creation of value for the end customer to be wasteful, and thus a target for elimination...
systems. Cellular Manufacturing is based upon the principals of Group Technology, which seeks to take full advantage of the similarity between parts, through standardisation and common processing. In Functional Manufacturing similar machines are placed close together (e.g. lathes, millers, drills etc.). Functional layouts are more robust to machine breakdowns, have common jigs and fixtures in the same area and supports high levels of demarcation. In Cellular Manufacturing systems machines are grouped together according to the families of parts produced. The major advantage is that material flow is significantly improved, which reduces the distance travelled by materials, inventory and cumulative lead times. Cellular Manufacturing employs setup reduction and gives the workers the tools to be multiprocess, operating multiple processes, and multifunctional, owning quality improvements, waste reduction, and simple machine maintenance. This allows workers to easily self-balance within the cell while reducing lead times, resulting in the ability for companies to manufacture high quality products at a low cost, on time, and in a flexible way.
The goal of lean manufacturing is the aggressive minimisation of waste, called muda, to achieve maximum efficiency of resources. Cellular manufacturing, sometimes called cellular or cell production, arranges factory floor labor into semi-autonomous and multi-skilled teams, or work cells, who manufacture complete products or complex components. Properly trained and implemented cells are more flexible and responsive than the traditional mass-production
Mass production
Mass production is the production of large amounts of standardized products, including and especially on assembly lines...
line, and can manage processes, defects, scheduling, equipment maintenance, and other manufacturing issues more efficiently.
History
Cellular Manufacturing is the application of the principles of Group Technology in manufacturing. Group Technology was proposed by Flanders in 1925 and adopted in Russia by Mitrofanov in 1933 (although the work was translated into English in 1966). Jack Burbidge (1978) did much to promote Group Technology in the UK. Although there appear to have been similar applications earlier in history Portsmouth Block MillsPortsmouth Block Mills
The Portsmouth Block Mills form part of the Portsmouth Dockyard at Portsmouth, Hampshire, England, and were built during the Napoleonic Wars to supply the British Royal Navy with pulley blocks. They started the age of mass-production using all-metal machine tools and are regarded as one of the...
offers what by definition constitutes an early example of cellular manufacturing. By 1808, using machinery designed by Marc Isambard Brunel
Marc Isambard Brunel
Sir Marc Isambard Brunel, FRS FRSE was a French-born engineer who settled in England. He preferred the name Isambard, but is generally known to history as Marc to avoid confusion with his more famous son Isambard Kingdom Brunel...
and constructed by Henry Maudslay
Henry Maudslay
Henry Maudslay was a British machine tool innovator, tool and die maker, and inventor. He is considered a founding father of machine tool technology.-Early life:...
, the Block Mills were producing 130,000 blocks (pulleys) for the Royal Navy
Royal Navy
The Royal Navy is the naval warfare service branch of the British Armed Forces. Founded in the 16th century, it is the oldest service branch and is known as the Senior Service...
per year in single unit lots, with 10 men operating 42 machines arranged in three production flow lines. This installation apparently reduced manpower requirements by 90% (from 110 to 10), reduced cost substantially and greatly improved block consistency and quality. Group Technology
Group technology
Group Technology or GT is a manufacturing philosophy in which the parts having similarities are grouped together to achieve higher level of integration between the design and manufacturing functions of a firm....
is a management strategy with long term goals of staying in business, growing, and making profits. Companies are under relentless pressure to reduce costs while meeting the high quality expectations of the customer to maintain a competitive advantage. Successfully implementing Cellular manufacturing allows companies to achieve cost savings and quality improvements, especially when combined with the other aspects of lean manufacturing. Cell manufacturing systems are currently used to manufacture anything from hydraulic and engine pumps used in aircraft to plastic packaging components made using injection molding.
Design
The goal of cellular manufacturing is having the flexibility to produce a high variety of low demand products, while maintaining the high productivity of large scale production. Cell designers achieve this through modularity in both process design and product design. Processes are arranged in a U-shape so that the beginning and end of the material flow within the cell are near each other. This allows quick rebalancing of tasks without redesigning stations, because workers can cross the aisle.Process design
The division of the entire production process into discrete segments, and the assignment of each segment to a work cell, introduces the modularity of processes. If any segment of the process needs to be changed, only the particular cell would be affected, not the entire production line. For example, if a particular component was prone to defects, and this could be solved by upgrading the equipment, a new work cell could be designed and prepared while the obsolete cell continued production. Once the new cell is tested and ready for production, the incoming parts to and outgoing parts from the old cell will simply be rerouted to the new cell without having to disrupt the entire production line. In this way, work cells enable the flexibility to upgrade processes and make variations to products to better suit customer demands while largely reducing or eliminating the costs of stoppages.While the machinery may be functionally dissimilar, the family of parts produced contains similar processing requirements or has geometric similarities. Thus, all parts basically follow the same routing with some minor variations (e.g., skipping an operation). The cells may have no conveyorized movement of parts between machines, or they may have a flow line connected by a conveyor that can provide automatic transfer.
Product design
Product modularity must match the modularity of processes. Even though the entire production system becomes more flexible, each individual cell is still optimised for a relatively narrow range of tasks, in order to take advantage of the mass-production efficiencies of specialisation and scale. To the extent that a large variety of products can be designed to be assembled from a small number of modular parts, both high product variety and high productivity can be achieved. For example, a varied range of automobiles may be designed to use the same chassis, a small number of engine configurations, and a moderate variety of car bodies, each available in a range of colors. In this way, a large variety of automobiles, with different performances and appearances and functions, can be produced by combining the outputs from a more limited number of work cells.In combination, each modular part is designed for a particular work cell, or dedicated clusters of machines or manufacturing processes. Cells are usually bigger than typical conventional workstations, but smaller than a complete conventional department. After conversion, a cellular manufacturing layout usually requires less floor space as a result of the optimized production processes. Each cell is responsible for its own internal control of quality, scheduling, ordering, and record keeping. The idea is to place the responsibility of these tasks on those who are most familiar with the situation and most able to quickly fix any problems. The middle management no longer has to monitor the outputs and interrelationships of every single worker, and instead only has to monitor a smaller number of work cells and the flow of materials between them, often achieved using a system of kanban
Kanban
, also spelled kamban, and literally meaning "signboard" or "billboard", is a concept related to lean and just-in-time production. According to Taiichi Ohno, the man credited with developing Just-in-time, kanban is one means through which JIT is achieved.Kanban is not an inventory control system...
s.
Implementation
The biggest challenge when implementing cellular manufacturing in a company is dividing the entire manufacturing system into cells. The issues may be conceptually divided in the "hard" issues of equipment, such as material flow and layout, and the "soft" issues of management, such as upskilling and corporate culture.gkjl;The hard issues are a matter of design and investment. The entire factory floor is rearranged, and equipment is modified or replaced to enable cell manufacturing. The costs of work stoppages during implementation can be considerable, and lean manufacturing literature recommend that implementation should be phased to minimize the impacts of such disruptions as much as possible. The rearrangement of equipment (which is sometimes bolted to the floor or built into the factory building) or the replacement of equipment that is not flexible or reliable enough for cell manufacturing also pose considerable costs, although it may be justified as the upgrading obsolete equipment. In both cases, the costs have to be justified by the cost savings that can be realistically expected from the more flexible cell manufacturing system being introduced, and miscalculations can be disastrous. A common oversight is the need for multiple jigs, fixtures and or tooling for each cell. Properly designed, these requirements can be accommodated in specific-task cells serving other cells; such as a common punch press or test station. Too often, however, the issue is discovered late and each cell is found to require its own set of tooling.
The soft issues are more difficult to calculate and control. The implementation of cell manufacturing often involves employee training and the redefinition and reassignment of jobs. Each of the workers in each cell should ideally be able to complete the entire range of tasks required from that cell, and often this means being more multi-skilled than they were previously. For this reason, transition from a progressive assembly line type of manufacturing to cellular is often best managed in stages with both types co-existing for a period of time. In addition, cells are expected to be self-managing (to some extent), and therefore workers will have to learn the tools and strategies for effective teamwork and management, tasks that workers in conventional factory environments are entirely unused to. At the other end of the spectrum, the management will also find their jobs redefined, as they must take a more "hands-off" approach to allow work cells to effectively self-manage. Instead, they must learn to perform a more oversight and support role, maintaining a system where work cells self-optimize through supplier-input-process-output-customer (SIPOC) relationships. These soft issues, while difficult to pin down, pose a considerable challenge for cell manufacturing implementation; a factory with a cell manufacturing layout but without cell manufacturing workers and managers is unlikely to achieve the cell manufacturing benefits.
Product start-ups can be more difficult to manage if assembly training was traditionally accomplished station-by-station on a fixed assembly line. As each operator in a cell is responsible for a larger number of assembled parts and operations, the time needed to master the sequence and techniques is considerably longer. If multiple parallel cells are used, each cell must be launched separately (meaning slower production ramp) or with equal training resources (meaning more in total). The consideration of the cell's internal group dynamics, personalities and other traits is often more of a concern in cellular manufacturing due to the closer proximity and co-dependency of the team members; however properly implemented this is a major benefit of cellular manufacturing.
Benefits and costs
There are many benefits of cellular manufacturing for a company if applied correctly. Most immediately, processes become more balanced and productivity increases because the manufacturing floor has been reorganized and tidied up.Part movement, set-up time, and wait time between operations are reduced, resulting in a reduction of work in progress inventory freeing idle capital that can be better utilized elsewhere. Cellular manufacturing, in combination with the other lean manufacturing and just-in-time processes, also helps eliminate overproduction by only producing items when they are needed. The results are cost savings and the better control of operations.
There are some costs of implementing cellular manufacturing, however, in addition to the set-up costs of equipment and stoppages noted above. Sometimes different work cells can require the same machines and tools, possibly resulting in duplication causing a higher investment of equipment and lowered machine utilization
Utilization
Utilization is a statistical concept as well as a primary business measure for the rental industry.-Queueing theory:In queueing theory, utilization is the proportion of the system's resources which is used by the traffic which arrives at it. It should be strictly less than one for the system to...
. However, this is a matter of optimization and can be addressed through process design.