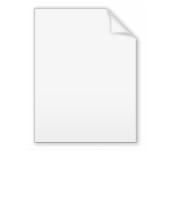
Buttwelding
Encyclopedia
Butt welding can be used to run a processing machine continuously, as opposed to having to restart such machine with a new supply of metals.
Usually, the seams (or abutment sections) are cleaned and prepared, and set on an automated piece of equipment which then welds the two materials together. Afterward, the material is usually ground down to a smooth finish and either sent on its way to the processing machine, or sold as a completed product.
This type of weld is usually accomplished with an arc or MIG welder, but can also be accomplished by brazing. With arc welding, after the butt weld is complete, the weld itself needs to be struck with a hammer forge to remove slag (a type of waste material) before any subsequent welds can be applied. This is not necessary for MIG welds however, as a protective gas removes any need for slag to appear. Another advantage with a MIG welder is that a continuous copper wire is fed onto the stock, making the weld virtually inexhaustible.
Usually, the seams (or abutment sections) are cleaned and prepared, and set on an automated piece of equipment which then welds the two materials together. Afterward, the material is usually ground down to a smooth finish and either sent on its way to the processing machine, or sold as a completed product.
This type of weld is usually accomplished with an arc or MIG welder, but can also be accomplished by brazing. With arc welding, after the butt weld is complete, the weld itself needs to be struck with a hammer forge to remove slag (a type of waste material) before any subsequent welds can be applied. This is not necessary for MIG welds however, as a protective gas removes any need for slag to appear. Another advantage with a MIG welder is that a continuous copper wire is fed onto the stock, making the weld virtually inexhaustible.