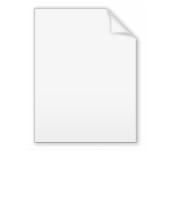
Baghouse
Encyclopedia
A baghouse or fabric filter (FF) is an air pollution control device that removes particulates out of air or gas released from commercial processes or combustion for electricity generation. Power plants, steel mills, pharmaceutical producers, food manufactures, chemical producers and other industrial companies often use baghouses to control emission of air pollutants. Baghouses came into widespread use in the late 1970s after the invention of high-temperature fabrics (for use in the filter media) capable of withstanding temperatures over 350°F.
Unlike electrostatic precipitators, where performance can vary significantly depending on process and electrical conditions, functioning baghouses typically have a particulate collection efficiency of 99% or better, even when particle size is very small.
Baghouses are very efficient particulate collectors because of the dust cake formed on the surface of the bags. The fabric provides a surface on which dust collects through the following four mechanisms:
A combination of these mechanisms results in formation of the dust cake on the filter, which eventually increases the resistance to gas flow. The filter must be cleaned periodically.
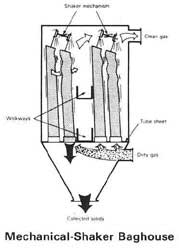
In mechanical-shaker baghouses, tubular filter bags are fastened onto a cell plate at the bottom of the baghouse and suspended from horizontal beams at the top. Dirty gas enters the bottom of the baghouse and passes through the filter, and the dust collects on the inside surface of the bags.
Cleaning a mechanical-shaker baghouse is accomplished by shaking the top horizontal bar from which the bags are suspended. Vibration produced by a motor-driven shaft and cam creates waves in the bags to shake off the dust cake.
Shaker baghouses range in size from small, handshaker devices to large, compartmentalized units. They can operate intermittently or continuously. Intermittent units can be used when processes operate on a batch basis-when a batch is completed, the baghouse can be cleaned. Continuous processes use compartmentalized baghouses; when one compartment is being cleaned, the airflow can be diverted to other compartments.
In shaker baghouses, there must be no positive pressure inside the bags during the shake cycle. Pressures as low as 0.02 in. wg can interfere with cleaning.
The air to cloth ratio
for shaker baghouses is relatively low, hence the space requirements are quite high. However, because of the simplicity of design, they are popular in the minerals processing industry.
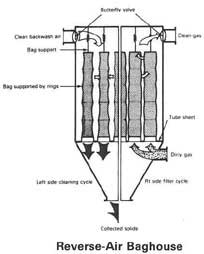
In reverse-air baghouses, the bags are fastened onto a cell plate at the bottom of the baghouse and suspended from an adjustable hanger frame at the top. Dirty gas flow normally enters the baghouse and passes through the bag from the inside, and the dust collects on the inside of the bags.
Reverse-air baghouses are compartmentalized to allow continuous operation. Before a cleaning cycle begins, filtration is stopped in the compartment to be cleaned. Bags are cleaned by injecting clean air into the dust collector in a reverse direction, which pressurizes the compartment. The pressure makes the bags collapse partially, causing the dust cake to crack and fall into the hopper below. At the end of the cleaning cycle, reverse airflow is discontinued, and the compartment is returned to the main stream.
The flow of the dirty gas helps maintain the shape of the bag. However, to prevent total collapse and fabric chafing during the cleaning cycle, rigid rings are sewn into the bags at intervals.
Space requirements for a reverse-air baghouse are comparable to those of a shaker baghouse; however, maintenance needs are somewhat greater.
In reverse-pulse-jet baghouses, individual bags are supported by a metal cage (filter cage), which is fastened onto a cell plate at the top of the baghouse. Dirty gas enters from the bottom of the baghouse and flows from outside to inside the bags. The metal cage prevents collapse of the bag.
Bags are cleaned by a short burst of compressed air injected through a common manifold over a row of bags. The compressed air is accelerated by a venturi
nozzle mounted at the reverse-jet baghouse top of the bag. Since the duration of the compressed-air burst is short (0.1s), it acts as a rapidly moving air bubble, traveling through the entire length of the bag and causing the bag surfaces to flex. This flexing of the bags breaks the dust cake, and the dislodged dust falls into a storage hopper below.
Reverse-pulse-jet dust collectors can be operated continuously and cleaned without interruption of flow because the burst of compressed air is very small compared with the total volume of dusty air through the collector. Because of this continuous-cleaning feature, reverse-jet dust collectors are usually not compartmentalized.
The short cleaning cycle of reverse-jet collectors reduces recirculation and redeposit of dust. These collectors provide more complete cleaning and reconditioning of bags than shaker or reverse-air cleaning methods. Also, the continuous-cleaning feature allows them to operate at higher air-to-cloth ratios, so the space requirements are lower.
This cleaning system works with the help of digital sequential timer attached to the fabric filter. this timer indicates the solenoid valve to inject the air to the blow pipe.
Some baghouses have sonic horns installed to provide supplementary vibration cleaning energy. The horns, which generate high intensity, low frequency sounds waves, are turned on just before or at the start of the cleaning cycle to help break the bonds between particles on the filter media surface and aid in dust removal.
Two main sequence types are used to clean baghouses:
Intermittently cleaned baghouses are composed of many compartments or sections. One at a time, each compartment is periodically closed off from the incoming dirty gas stream, cleaned, and then brought back online. While the individual compartment is out of place, the gas stream is diverted from the compartment’s area. This makes shutting down the production process unnecessary during cleaning cycles.
Continuously cleaned baghouse compartments are always online for automatic filtering. A blast of compressed air momentarily interrupts the collection process to clean the bag. This is known as pulse jet cleaning. Pulse jet cleaning does not require taking compartments offline. Continously cleaned baghouses are designed to prevent complete shutdown during bag maintenance and failures to the primary system.
Nonwoven materials are either felted or membrane. Nonwoven materials are attached to a woven backing (scrim). Felted filters contain randomly placed fibers supported by a woven backing material (scrim). In a membrane filter, a thin, porous membrane is bound to the scrim. High energy cleaning techniques such as pulse jet require felted fabrics.
Woven filters have a definite repeated pattern. Low energy cleaning methods such as shaking or reverse air allow for woven filters. Various weaving patterns such as plain weave, twill weave, or sateen weave, increase or decrease the amount of space between individual fibers. The size of the space affects the strength and permeability of the fabric. A tighter weave corresponds with low permeability and, therefore, more efficient capture of fine particles.
Reverse air bags have have anti-collapse rings sewn into them to prevent pancaking when cleaning energy is applied. Pulse jet filter bags are supported by a metal cage, which keeps the fabric taut. To lengthen the life of filter bags, a thin layer of PTFE (teflon) membrane may be adhered to the filtering side of the fabric, keeping dust particles from becoming embedded in the filter media fibers.
Some baghouses use pleated cartridge filters, similar to what is found in home air filtration systems.
Unlike electrostatic precipitators, where performance can vary significantly depending on process and electrical conditions, functioning baghouses typically have a particulate collection efficiency of 99% or better, even when particle size is very small.
Operation of Baghouses
Most baghouses use long, cylindrical bags (or tubes) made of woven or felted fabric as a filter medium. (For applications where there is relatively low dust loading and gas temperatures are 250°F or less, pleated, nonwoven cartridges are sometimes used as filtering media instead of bags.) Dust-laden gas or air enters the baghouse through hoppers (large funnel-shaped containers used for storing and dispensing particulate) and is directed into the baghouse compartment. The gas is drawn through the bags, either on the inside or the outside depending on cleaning method, and a layer of dust accumulates on the filter media surface until air can no longer move through it. When sufficient pressure drop (delta P) occurs, the cleaning process begins. Cleaning can take place while the baghouse is online (filtering) or is offline (in isolation). When the compartment is clean, normal filtering resumes.Baghouses are very efficient particulate collectors because of the dust cake formed on the surface of the bags. The fabric provides a surface on which dust collects through the following four mechanisms:
- Inertial collection - Dust particles strike the fibers placed perpendicular to the gas-flow direction instead of changing direction with the gas stream.
- Interception - Particles that do not cross the fluid streamlines come in contact with fibers because of the fiber size.
- Brownian movement - Submicrometre particles are diffused, increasing the probability of contact between the particles and collecting surfaces.
- Electrostatic forces - The presence of an electrostatic charge on the particles and the filter can increase dust capture.
A combination of these mechanisms results in formation of the dust cake on the filter, which eventually increases the resistance to gas flow. The filter must be cleaned periodically.
Types of Baghouses - Cleaning Methods
Baghouses are classified by the cleaning method used. The three most common types of baghouses are mechanical shakers, reverse gas, and pulse jet.Mechanical Shaker Baghouses
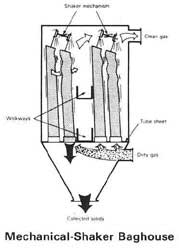
In mechanical-shaker baghouses, tubular filter bags are fastened onto a cell plate at the bottom of the baghouse and suspended from horizontal beams at the top. Dirty gas enters the bottom of the baghouse and passes through the filter, and the dust collects on the inside surface of the bags.
Cleaning a mechanical-shaker baghouse is accomplished by shaking the top horizontal bar from which the bags are suspended. Vibration produced by a motor-driven shaft and cam creates waves in the bags to shake off the dust cake.
Shaker baghouses range in size from small, handshaker devices to large, compartmentalized units. They can operate intermittently or continuously. Intermittent units can be used when processes operate on a batch basis-when a batch is completed, the baghouse can be cleaned. Continuous processes use compartmentalized baghouses; when one compartment is being cleaned, the airflow can be diverted to other compartments.
In shaker baghouses, there must be no positive pressure inside the bags during the shake cycle. Pressures as low as 0.02 in. wg can interfere with cleaning.
The air to cloth ratio
Air to cloth ratio
The air-to-cloth ratio is the volumetric flow rate of air flowing through a dust collector's inlet duct divided by the total cloth area in the filters...
for shaker baghouses is relatively low, hence the space requirements are quite high. However, because of the simplicity of design, they are popular in the minerals processing industry.
Reverse Air (R/A) Baghouses (aka Reverse Gas)
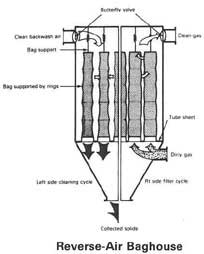
In reverse-air baghouses, the bags are fastened onto a cell plate at the bottom of the baghouse and suspended from an adjustable hanger frame at the top. Dirty gas flow normally enters the baghouse and passes through the bag from the inside, and the dust collects on the inside of the bags.
Reverse-air baghouses are compartmentalized to allow continuous operation. Before a cleaning cycle begins, filtration is stopped in the compartment to be cleaned. Bags are cleaned by injecting clean air into the dust collector in a reverse direction, which pressurizes the compartment. The pressure makes the bags collapse partially, causing the dust cake to crack and fall into the hopper below. At the end of the cleaning cycle, reverse airflow is discontinued, and the compartment is returned to the main stream.
The flow of the dirty gas helps maintain the shape of the bag. However, to prevent total collapse and fabric chafing during the cleaning cycle, rigid rings are sewn into the bags at intervals.
Space requirements for a reverse-air baghouse are comparable to those of a shaker baghouse; however, maintenance needs are somewhat greater.
Pulse Jet Baghouses (aka Reverse Jet)
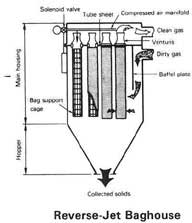
Bags are cleaned by a short burst of compressed air injected through a common manifold over a row of bags. The compressed air is accelerated by a venturi
Venturi effect
The Venturi effect is the reduction in fluid pressure that results when a fluid flows through a constricted section of pipe. The Venturi effect is named after Giovanni Battista Venturi , an Italian physicist.-Background:...
nozzle mounted at the reverse-jet baghouse top of the bag. Since the duration of the compressed-air burst is short (0.1s), it acts as a rapidly moving air bubble, traveling through the entire length of the bag and causing the bag surfaces to flex. This flexing of the bags breaks the dust cake, and the dislodged dust falls into a storage hopper below.
Reverse-pulse-jet dust collectors can be operated continuously and cleaned without interruption of flow because the burst of compressed air is very small compared with the total volume of dusty air through the collector. Because of this continuous-cleaning feature, reverse-jet dust collectors are usually not compartmentalized.
The short cleaning cycle of reverse-jet collectors reduces recirculation and redeposit of dust. These collectors provide more complete cleaning and reconditioning of bags than shaker or reverse-air cleaning methods. Also, the continuous-cleaning feature allows them to operate at higher air-to-cloth ratios, so the space requirements are lower.
This cleaning system works with the help of digital sequential timer attached to the fabric filter. this timer indicates the solenoid valve to inject the air to the blow pipe.
Type | Advantages | Disadvantages |
---|---|---|
Shaker Baghouses | Have high collection effiency for respirable dust | Have low air-to-cloth ratio (1.5 to 2 ft/min) |
Can use strong woven bags, which can withstand intensified cleaning cycle to reduce residual dust buildup | Cannot be used in high temperatures | |
Simple to operate | Require large amounts of space | |
Have low pressure drop for equivalent collection efficiencies | Need large numbers of filter bags | |
Consist of many moving parts and require frequent maintenance | ||
Personnel must enter baghouse to replace bags, creating potential for exposure to toxic dust | ||
Can result in reduced cleaning efficiency if even a slight positive pressure exists inside bags | ||
Reverse Air Baghouses | Have high collection efficiency for respirable dust | Have low air-to-cloth ratio (1 to 2 ft/min) |
Are preferred for high temperatures due to gentle cleaning action | Require frequent cleaning because of gentle cleaning action | |
Have low pressure drop for equivalent collection efficiencies | Have no effective way to remove residual dust buildup | |
Cleaning air must be filtered | ||
Require personnel to enter baghouse to replace bags which creates potential for toxic dust exposure | ||
Pulse Jet (Reversed Jet) Baghouses | Have high collection efficiency for respirable dust | Require use of dry compressed air |
Can have high air-to-cloth ratio (6 to 10 ft/min) | May not be used readily in high temperatures unless special fabrics are used | |
Have increased efficiency and minimal residual dust buildup due to aggressive cleaning action | Cannot be used if high moisture content or himidity levels are present in the exhauset gases | |
Can clean continuously | ||
Can use strong woven bags | ||
Have lower bag wear | ||
Have small size and fewer bags because of high air-to-cloth ratio | ||
Some designs allow bag changing without entering baghouse | ||
Have low pressure drop for equivalent collection efficiencies |
Sonic Horns
Some baghouses have sonic horns installed to provide supplementary vibration cleaning energy. The horns, which generate high intensity, low frequency sounds waves, are turned on just before or at the start of the cleaning cycle to help break the bonds between particles on the filter media surface and aid in dust removal.
Cleaning Sequences
Two main sequence types are used to clean baghouses:
- Intermittent (periodic) cleaning
- Continuous cleaning.
Intermittently cleaned baghouses are composed of many compartments or sections. One at a time, each compartment is periodically closed off from the incoming dirty gas stream, cleaned, and then brought back online. While the individual compartment is out of place, the gas stream is diverted from the compartment’s area. This makes shutting down the production process unnecessary during cleaning cycles.
Continuously cleaned baghouse compartments are always online for automatic filtering. A blast of compressed air momentarily interrupts the collection process to clean the bag. This is known as pulse jet cleaning. Pulse jet cleaning does not require taking compartments offline. Continously cleaned baghouses are designed to prevent complete shutdown during bag maintenance and failures to the primary system.
Baghouse Performance
Baghouse performance is contingent upon inlet and outlet gas temperature, pressure drop, opacity, and gas velocity. The chemical composition, moisture, acid dew point, and particle loading and size distribution of the gas stream are essential factors as well- Gas Temperature - Fabrics are designed to operate within a certain range of temperature. Fluctuation outside of these limits even for a small period of time, can weaken, damage, or ruin the bags.
- Pressure Drop - Baghouses operate most effectively within a certain pressure drop range. This spectrum is based on a specific gas volumetric flow rate.
- OpacityOpacity (optics)Opacity is the measure of impenetrability to electromagnetic or other kinds of radiation, especially visible light. In radiative transfer, it describes the absorption and scattering of radiation in a medium, such as a plasma, dielectric, shielding material, glass, etc...
- Opacity measures the quantity of light scattering that occurs as a result of the particles in a gas stream. Opacity is not an exact measurement of the concentration of particles; however, it is a good indicator of the amount of dust leaving the baghouse. - Gas Volumetric Flow Rate - Baghouses are created to accommodate a range of gas flows. An increase in gas flow rates causes an increase in operating pressure drop and air-to-cloth ratio. These increases require the baghouse to work more strenuously, resulting in more frequent cleanings and high particle velocity, two factors that shorten bag life.
Baghouse Design Variables
Pressure drop, filter drag, air-to-cloth ratio, and collection efficiency are essential factors in the design of a baghouse.- Pressure drop is the resistance to air flow across the baghouse. A high pressure drop corresponds with a higher resistance to airflow. Pressure drop is calculated by determining the difference in total pressure at two points, typically the inlet and outlet.
- Filter drag is the resistance across the fabric-dust layer. It is the pressure drop per unit of velocity.
- An understanding of the term air-to-cloth ratio is vital to understand the mechanics of any baghouse system regardless of the exact type used. This ratio is defined as the amount of air or process gas entering the Baghouse divided by the sq. ft of cloth in the Baghouse. Units of measure are (ft3/min)/ft2 or (cm3/sec)/cm2.
- Commonly, baghouses are designed with 99.9% collection efficiency. Oftentimes, cleaned air is recirculated back into the plant for heating.
Baghouse Filter Media
Fabric filter bags (sometimes referred to as envelopes) are oval or round tubes, typically 15-30 feet and 5 to 12 inches in diameter, made of woven or felted material. Depending on chemical and/or moisture content of the gas stream, its temperature, and other conditions, bags may be constructed out of cotton, nylon, polyester, fiberglass or other materials.Nonwoven materials are either felted or membrane. Nonwoven materials are attached to a woven backing (scrim). Felted filters contain randomly placed fibers supported by a woven backing material (scrim). In a membrane filter, a thin, porous membrane is bound to the scrim. High energy cleaning techniques such as pulse jet require felted fabrics.
Woven filters have a definite repeated pattern. Low energy cleaning methods such as shaking or reverse air allow for woven filters. Various weaving patterns such as plain weave, twill weave, or sateen weave, increase or decrease the amount of space between individual fibers. The size of the space affects the strength and permeability of the fabric. A tighter weave corresponds with low permeability and, therefore, more efficient capture of fine particles.
Reverse air bags have have anti-collapse rings sewn into them to prevent pancaking when cleaning energy is applied. Pulse jet filter bags are supported by a metal cage, which keeps the fabric taut. To lengthen the life of filter bags, a thin layer of PTFE (teflon) membrane may be adhered to the filtering side of the fabric, keeping dust particles from becoming embedded in the filter media fibers.
Some baghouses use pleated cartridge filters, similar to what is found in home air filtration systems.
Components of a Baghouse
- Bags, fabric & support
- Housing or shell
- Collection hoppers
- Discharge devices
- Filter cleaning device