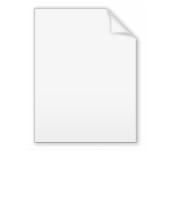
Automated Storage and Retrieval System
Encyclopedia
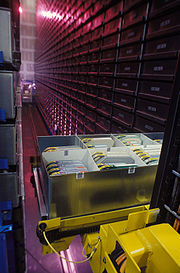

Overview
AS/RS systems are devices designed for automated storage and retrieval of parts and items in manufacturing, distribution, retail, wholesale and institutions. They focus on bringing "goods to the man" rather than manual walking and searching. Space savings, increased productivity/reduced labor, increased accuracy and reduced inventory levels are some of the primary benefits. Ideal for lean manufacturingLean manufacturing
Lean manufacturing, lean enterprise, or lean production, often simply, "Lean," is a production practice that considers the expenditure of resources for any goal other than the creation of value for the end customer to be wasteful, and thus a target for elimination...
, sustainability
Sustainability
Sustainability is the capacity to endure. For humans, sustainability is the long-term maintenance of well being, which has environmental, economic, and social dimensions, and encompasses the concept of union, an interdependent relationship and mutual responsible position with all living and non...
, six sigma
Six Sigma
Six Sigma is a business management strategy originally developed by Motorola, USA in 1986. , it is widely used in many sectors of industry.Six Sigma seeks to improve the quality of process outputs by identifying and removing the causes of defects and minimizing variability in manufacturing and...
, Kanban
Kanban
, also spelled kamban, and literally meaning "signboard" or "billboard", is a concept related to lean and just-in-time production. According to Taiichi Ohno, the man credited with developing Just-in-time, kanban is one means through which JIT is achieved.Kanban is not an inventory control system...
, JIT and other value added methodologies and processes. The equipment required for an AS/RS include a Storage & Retrieval Machine, or SRM, that is used for rapid storage and retrieval of material. SRM are used to move loads vertically or horizontally. SRM can also move laterally to place objects in correct storage location.
The traditional vending machine is the most common and familiar AS/RS system but because the application is to do with retail sales, the logistic concept of a vending machine is missed.
The trend towards just in time production often requires sub-pallet level availability of production inputs, and AS/RS is a much faster way of organizing the storage of smaller items next to production lines. Traditional high bay warehouses are designed with pallet storage in mind, and if goods are being delivered in sub pallet quantities, high bay warehouses are problematic.
Material Handling Institute of America (MHIA), the non-profit trade association for the material handling world, and its members have broken AS/RS into two primary segments: Fixed Aisle and Carousels/Vertical Lift Modules (VLMs). Both sets of technologies provide automated storage and retrieval for parts and items, but use different technologies. Each technology has its unique set of benefits and disadvantages (like everything in the world). Fixed Aisle systems are characteristically larger systems where as carousels and Vertical Lift Modules are used individually or grouped, but in small to medium-sized applications.
Fixed-aisle AS/RS is categorized into three main types: single-masted, double masted, and man-aboard. Most are supported on a track and ceiling guided at the top by guide rails or channels to ensure accurate vertical alignment, although some are suspended from the ceiling. The 'shuttles' that make up the system travel between fixed storage shelves to deposit or retrieve a requested load (ranging from a single book in a library system to a several ton pallet of goods in a warehouse system). As well as moving along the ground, the shuttles are able to telescope up to the necessary height to reach the load, and can store or retrieve loads that are several positions deep in the shelving. A semi-automated system can be achieved by utilizing only specialized shuttles within an existing rack system.
To provide a method for accomplishing throughput to and from the AS/RS and the supporting transportation system, stations are provided to precisely position inbound and outbound loads for pickup and delivery by the crane.
In addition, there are five types of AS/RS devices called Unit-load AS/RS, Mini-load AS/RS, Vertical Lift Modules (VLMs), Horizontal Carousels and Vertical Carousels. These systems are used either as stand-alone units or in integrated workstations called pods. These units usually are integrated with various types of pick to light systems and use either a microprocessor controller for basic usage or inventory management software. These systems are ideal for increasing space utilization up to 85%, productivity levels by 2/3, accuracy to 99.9%+ levels and throughput up to 750 lines per hour/per operator.
Man-aboard AS/RS
A man-aboard AS/RS offers significant floorspace savings. This is due to the fact that the storage system heights are no longer limited by the reach height of the order picker. Shelves or storage cabinets can be stacked as high as floor loading, weight capacity, throughput requirements, and/or ceiling heights will permit. Man-aboard automated storage and retrieval systems are far and away the most expensive picker-to-stock equipment alternative. Aisle-captive storage/retrieval machines reaching heights up to 40 feet cost around $125,000. Hence, there must be enough storage density and/or productivity improvement over cart and tote picking to justify the investment. Also, because vertical travel is slow compared to horizontal travel, typical picking rates in man-aboard operations range between 40 and 250 lines per person-hour. The range is large because there is a wide variety of operating schemes for man-aboard systems. Man-aboard systems are typically appropriate for slow-moving items where space is fairly expensive.Vertical Lift Module
The VLM is a computer controlled automated vertical lift module, storage and retrieval system. Functionally, stock within the VLM remains stationary on front and rear tray locations. On request a movable extractor unit travels vertically between the two columns of trays and pulls the requested tray from its location and brings it to an access point. The operator then picks or replenishes stock and the tray is returned to its home.VLM system offers variable tray sizes and loads, which could be applied in different industries, logistic, as well as office settings. The VLM systems could be customized to fully utilize the height of the facility, even through multiple floors. With the capability of multiple access openings on different floors, the VLM system is able to provide an innovative storage and retrieval solution. The rapid movement of the extractor as well as the integrated inventory management software can dramatically increase the efficiency of the picking process. Unlike large AS/RS systems, which require a complete overhaul of the warehouse or production line, the Vertical Lift Module are modularized, which can be easily integrated into the existing system, or to be rolled out in gradually over different phases.
This is the first model of the same.
Most common applications include: MRO, order picking, consolidation, kitting, parts handling, buffering, inventory storage, WIP, buffer storage, and many more.
The labor (up to 2/3) and space saving benefits (up to 85%) are primary needs.
Most VLMs offer dynamic space storage which measures the tray every time it's returned to the unit to optimize space, tilt tray delivery for increased ergonomic accessibility, and laser pointers which indicate the exact item to be picked on each tray.
Horizontal Carousels
A horizontal carousel is a series of bins which rotate on an oval track. Every bin has shelves which are adjustable to .75" and can be configured for a myriad of standard and special applications. An operator simply inputs a bin number, part number or cell location and the carousel will rotate via the shortest path. Multiple horizontal carousels integrated with pick to light technology and inventory management software (a pod of carousels) are used for order fulfillment.A wave of orders are sent to the pod. A group of orders are selected to create a batch. The operator simply follows the lights and pick round robin from the carousels and place items in a batch station behind them. Each carousel pre-positions and rotates when picked. By applying the "product to picker" principle, operators do not have to move from their position to prepare the order.
When the batch is complete, a new batch is inducted and the process repeated until the wave is complete. Horizontal carousels can save up to 75% of floorspace, increase productivity by 2/3, accuracy levels to 99.9%+ levels and throughput up to 750 lines per hour/operator.
Horizontal carousel systems generally outperform robotic systems for a fraction of the cost. Horizontal carousels are the most cost effective AS/RS system available.
On a simplistic level, horizontal carousels are also often used as "rotating shelving." 'With simple "fetch" command items are brought to the operator and otherwise wasted space is eliminated.
Installed Applications
Installed applications of this technology can be wide ranging. In some libraries, such as at UNRUNR
UNR can mean:* National University of Rwanda * University of Nevada, Reno* Universidad Nacional de Rosario, National University of Rosario, Argentina...
library, such a system is employed to retrieve books. Still others in use involve retrieval of bicycles from a bicycle tree
Bicycle tree
A Bicycle tree or cycle tree or bike tree is an bicycle parking system that resembles a tree in shape. There are a few types that have been developed....
, as in the case of systems in Japan.
See also
- Actionable information logisticsActionable information logisticsActionable information logistics is the supply of immediately available informations to users necessary for them to deal with the situation at hand-Origin:...
- Autonomous logisticsAutonomous logisticsAutonomous logistics describes systems that provide unmanned, autonomous transfer of equipment, baggage, people, information or resources from point-to-point with minimal intervention...
- Inventory management softwareInventory management softwareInventory management software is a computer-based system for tracking product levels, orders, sales and deliveries. It can also be used in the manufacturing industry to create a work order, bill of materials and other production-related documents. Companies use inventory management software to...
- Voice Directed WarehousingVoice Directed WarehousingVoice-directed warehousing refers to the use of the voice direction and speech recognition software in warehouses and distribution centers...
- WarehouseWarehouseA warehouse is a commercial building for storage of goods. Warehouses are used by manufacturers, importers, exporters, wholesalers, transport businesses, customs, etc. They are usually large plain buildings in industrial areas of cities and towns. They usually have loading docks to load and unload...